Filtro de espuma de carburo de silicio
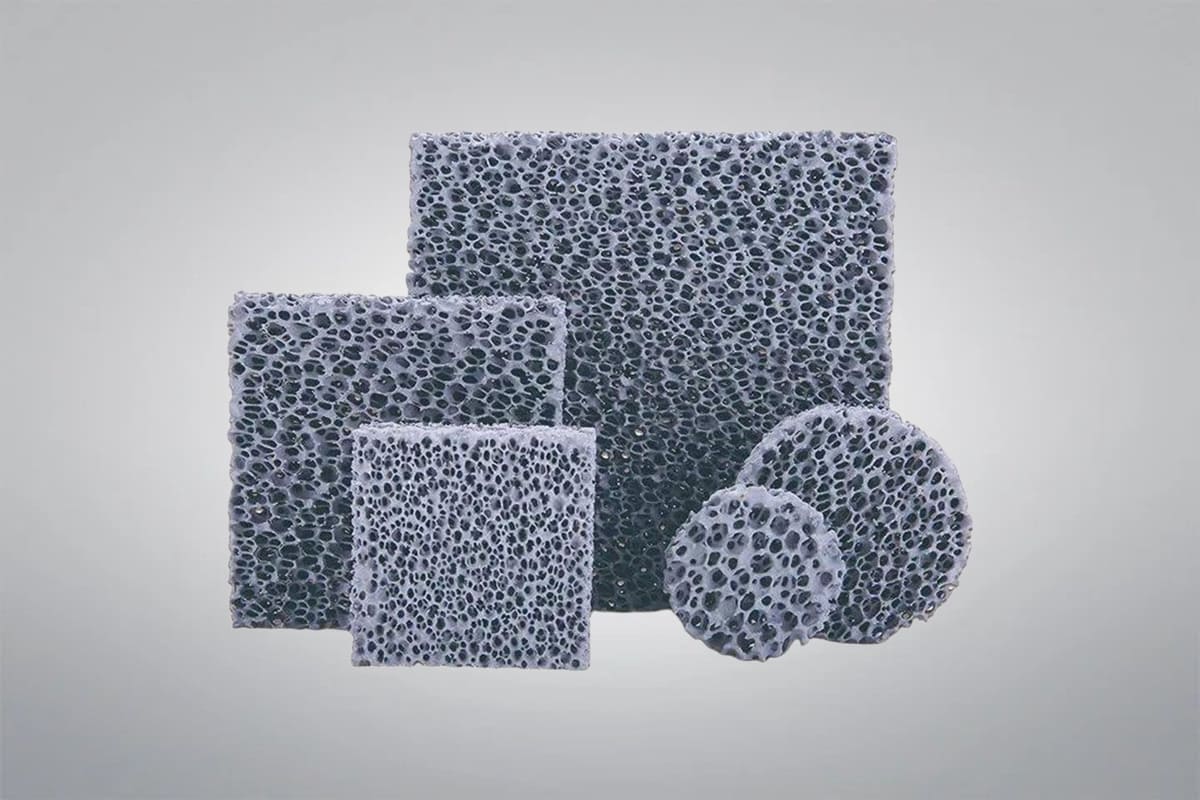
Filtro de espuma de carburo de silicio
Porosidad: 80%-90%
Tamaño de la célula: 7-45 PPI
El filtro de espuma de carburo de silicio es un material de filtración de alto rendimiento con excelente resistencia a altas temperaturas (hasta 1500℃), resistencia a la corrosión química y alta resistencia mecánica. Se utiliza ampliamente en fundición de metales, química y medio ambiente. Como proveedor y fabricante líder de productos de carburo de silicio de primera calidad, podemos suministrar filtros de espuma de carburo de silicio de alta calidad con varias especificaciones y precios competitivos, ofreciendo soluciones personalizadas para satisfacer requisitos específicos.
O envíenos un correo electrónico a sales@heegermaterials.com.Hoja de datos del filtro de espuma de carburo de silicio
Código de referencia: | HM3012 |
Composición química: | SiC, Al2O3, SiO2 |
Porosidad: | 80%-90% |
Tamaño del poro: | 7-45 PPI |
Temperatura de funcionamiento: | ≤1500℃ |
Densidad de volumen: | 0,4-0,5 g/cm3 |
Resistencia a la flexión a temperatura ambiente: | 0,8 MPa |
Resistencia a la compresión a temperatura ambiente: | 1,0 MPa |
Resistencia al choque térmico: | 1100℃ a temperatura ambiente, 6 veces |
Filtro de espuma de carburo de silicio Descripción
El filtro de espuma de carburo de silicio es un eficaz filtro de metal fundido con una estructura porosa única, que elimina eficazmente las impurezas y los gases del metal fundido y mejora la calidad de la fundición. Ofrece una excelente resistencia a altas temperaturas (hasta 1500℃), resistencia química y alta resistencia mecánica, por lo que es ideal para filtrar aluminio, cobre, hierro, etc. Las porosidades comunes son 10 PPI, 20 PPI, 30 PPI y 40 PPI. Avanzado Cerámica Cubo admite soluciones personalizadas en tamaños, grosores y poros para diversas aplicaciones industriales y de investigación.
Especificaciones del filtro de espuma de carburo de silicio
Dimensiones (mm) | Superficie (mm²) | Índice de porosidad (10/15ppi) | Índice de porosidad (20ppi) | Índice de porosidad (30ppi) | |
Longitud×Anchura×Grosor | 40×40×11, 13, 15, 22 | 1600 | ✓ | ✓ | ✓ |
50×50×11, 13, 15, 22 | 2500 | ✓ | ✓ | ||
50×75×13, 15, 22 | 3750 | ✓ | ✓ | ||
50×100×15, 22 | 5000 | ✓ | ✓ | ||
55×55×22 | 3025 | ✓ | |||
60×60×22 | 3600 | ✓ | ✓ | ||
75×75×22 | 5625 | ✓ | ✓ | ||
75×100×22 | 7500 | ✓ | |||
100×100×22 | 10000 | ✓ | ✓ | ||
100×150×22 | 15000 | ✓ | ✓ | ||
150×150×22 | 22500 | ✓ | |||
Diámetro×Espesor | Φ 40×15 | 1526 | ✓ | ||
Φ 40×22 | 1526 | ✓ | |||
Φ 50×13, 15 | 1923 | ✓ | |||
Φ 50×22 | 1923 | ✓ | |||
Φ 60×18 | 2826 | ✓ | |||
Φ 60×22 | 2826 | ✓ | |||
Φ 70×22 | 3847 | ✓ | |||
Φ 1000 ×22 | 31400 | ✓ |
¿Cómo elegir el tamaño adecuado del filtro de espuma de carburo de silicio?
Aleación / Proceso | Unidad Superficie Cantidad de hierro / R (kg/cm²) |
Hierro gris, aleación de cobre y aluminio | 3.2 ~ 4.2 |
Grafito esferoidal Hierro | 1.6 ~ 2.1 |
Fundición refrigerada | 0.8 |
Embarazada In-Mold | 0.8 |
- Calcular la superficie efectiva requerida del filtro (área a través de la cual fluye el metal fundido) utilizando la fórmula S=G/R, donde G es el metal fundido total a filtrar, y R es la capacidad de filtración del filtro por unidad de superficie.
- Verifique el área efectiva contra el área de restricción de flujo del sistema de vertido. La relación recomendada es de 1:3 para fundición dúctil, y de 1:2 para fundición gris y fundición nodular.
- Añada el área del borde de apoyo (normalmente de 5 a 15 mm) para determinar el área total de filtrado necesaria y, a continuación, elija el tamaño y la cantidad del filtro en función del área total y las especificaciones del modelo.
- Alternativamente, el tamaño y la cantidad del filtro pueden determinarse teniendo en cuenta el peso del metal fundido, el número de canales interiores, la capacidad de filtración y las especificaciones del filtro.
- Los filtros más gruesos ofrecen mayor resistencia y eficacia, pero a un coste más elevado. Para un rendimiento óptimo, los espesores recomendados son: 15-22 mm para tamaños de 40-75 mm, 22-25 mm para tamaños de 75-120 mm, 25-30 mm para tamaños de 120-150 mm y 30-40 mm para tamaños superiores a 150 mm.
¿Cómo elegir el tamaño de poro adecuado del filtro de espuma de carburo de silicio?
La selección del tamaño de los poros del filtro de espuma de carburo de silicio depende principalmente del material del metal fundido, la temperatura de vertido, el tamaño de la colada y la pureza del metal fundido. Dado que los diferentes materiales del metal fundido tienen características de flujo variables, la elección del tamaño de poro puede variar significativamente.
- Las fundiciones de hierro dúctil suelen utilizar productos de 10 PPI o 15 PPI.
- El hierro gris y el cobre fundido suelen utilizar productos de 15 PPI o 20 PPI.
- Las fundiciones de aleaciones de aluminio suelen utilizar productos de 20 PPI o 30 PPI.
- La fundición nodular suele utilizar productos de 30 PPI.
Filtro de espuma de carburo de silicio Capacidad de filtración
Tamaño (mm) | 10ppi | 20ppi | 30ppi | |||
Capacidad del filtro (kg) | Caudal (Kg/s) | Capacidad del filtro (kg) | Caudal (kg/s) | Capacidad del filtro (kg) | Caudal (kg/s) | |
Hierro gris | Hierro gris | Hierro gris | Hierro gris | Hierro gris | Hierro gris | |
40×40×15 | 64 | 4 | 50 | 3 | 42 | 2 |
40×40×22 | 64 | 4 | 50 | 3 | 42 | 2 |
50×30×22 | 60 | 4 | 47 | 3 | 40 | 2 |
50×50×15 | 100 | 6 | 78 | 3.5 | 66 | 3 |
50×50×22 | 100 | 6 | 78 | 3.5 | 66 | 3 |
60×60×15 | 144 | 9 | 112 | 6 | 95 | 5 |
75×50×22 | 150 | 9 | 116 | 6 | 99 | 5 |
75×75×22 | 220 | 14 | 175 | 10 | 149 | 8 |
100×50×22 | 200 | 12 | 155 | 9 | 133 | 7 |
100×75×22 | 300 | 18 | 232 | 13 | 199 | 11 |
100×100×22 | 400 | 24 | 310 | 18 | 265 | 15 |
150×150×22 | 900 | 54 | 698 | 40 | 596 | 33 |
200×200×30 | 1600 | 95 | 1240 | 58 | 1060 | 48 |
Dia 40×22 | 40 | 3 | 39 | 2 | 33 | 2 |
Dia 50×22 | 70 | 4.5 | 61 | 4 | 52 | 3 |
Dia 60×22 | 100 | 6.5 | 88 | 5 | 75 | 4 |
Dia 70×22 | 150 | 8.8 | 119 | 7 | 102 | 6 |
Dia 75×22 | 170 | 10 | 137 | 8 | 117 | 6.5 |
Dia 80×22 | 200 | 11 | 156 | 9 | 133 | 7 |
Dia 90×22 | 240 | 14 | 197 | 11 | 169 | 9 |
Diámetro 100×22 | 280 | 17 | 243 | 14 | 208 | 12 |
Dia 125×22 | 400 | 24 | 380 | 22 | 325 | 18 |
Diámetro 150×22 | 700 | 38 | 548 | 32 | 468 | 26 |
Dia 200×30 | 1240 | 67 | 973 | 56 | 832 | 46 |
Características del filtro de espuma de carburo de silicio
- Alta estabilidad térmica: Pueden soportar altas temperaturas (hasta 1500℃), lo que las hace adecuadas para la filtración de metal fundido.
- Alta resistencia: Ofrece una excelente resistencia mecánica, garantizando la durabilidad durante el vertido del metal.
- Buena eficacia de filtración: Filtra eficazmente las impurezas, mejorando la calidad del metal.
- Baja caída de presión: Garantiza un flujo suave del metal fundido al tiempo que minimiza la pérdida de presión.
- Resistencia a la corrosión: Resistente a la corrosión por metales fundidos, prolongando la vida útil del filtro.
- Ligero y fácil de manejar: A pesar de su resistencia, son ligeras y fáciles de manejar.
- Control de la porosidad: Puede fabricarse con porosidad controlada para necesidades específicas de filtración.
Aplicaciones del filtro de espuma de carburo de silicio
- Metalurgia: Se utiliza en las fundiciones para filtrar metales fundidos como el hierro, el acero y las aleaciones no ferrosas, mejorando la pureza del metal y la calidad de la fundición.
- Fundición: Se utiliza para refinar la calidad de las piezas fundidas, reducir defectos como la porosidad y mejorar el acabado superficial.
- Industria siderúrgica: Ayuda a fabricar acero de alta calidad filtrando el acero fundido antes de la colada.
- Fundición de aluminio: Ampliamente utilizado en aluminio y sus aleaciones para eliminar impurezas y mejorar la integridad de la fundición.
- Industria del automóvil: Se utiliza para fabricar componentes como bloques de motor y otras piezas de fundición de vehículos.
Propiedades del material de carburo de silicio
Grados del material de carburo de silicio
El carburo de silicio aglomerado por reacción (RBSiC) se fabrica mezclando SiC, carbono y aglutinante y, a continuación, se infiltra con silicio a alta temperatura. El método de fase de vapor reduce el silicio libre a menos de 10%, lo que mejora el rendimiento. El resultado es un compuesto de silicio y carburo de silicio (SiSiC), no SiC puro.
Polvo de SiC + polvo de C + aglutinante mezclados → conformado → secado → atmósfera protectora para desgasificación → infiltración de silicio a alta temperatura → postprocesado.
Ventajas del SiC aglomerado por reacción:
- Baja temperatura de sinterización
- Bajo coste de producción
- Alta densificación del material
- La estructura de carbono y carburo de silicio puede premecanizarse en cualquier forma
- La contracción durante la sinterización es inferior a 3%, lo que facilita el control dimensional.
- Reducción significativa de la necesidad de acabado, ideal para componentes grandes y complejos
Desventajas del SiC aglomerado por reacción:
- Silicio libre residual en el cuerpo sinterizado tras la transformación
- Resistencia reducida en comparación con los productos de otros procesos
- Menor resistencia al desgaste
- El silicio libre no es resistente a la corrosión por sustancias alcalinas y ácidos fuertes (por ejemplo, ácido fluorhídrico).
- Uso limitado debido a la susceptibilidad a la corrosión
- La resistencia a altas temperaturas se ve afectada por el silicio libre
- La temperatura típica de uso se limita a menos de 1350-1400°C
El carburo de silicio sinterizado sin presión se refiere a la sinterización por densificación de muestras con formas y tamaños variables a 2000-2150°C sin aplicar presión externa y utilizando una atmósfera de gas inerte, mediante la incorporación de aditivos de sinterización adecuados. El proceso de sinterización puede clasificarse en sinterización en fase sólida (SSiC) y sinterización en fase líquida (LSiC).
Propiedades del SiC sinterizado en fase sólida (SSiC):
- Alta temperatura de sinterización: Requiere una temperatura de sinterización elevada (>2000°C).
- Requisito de gran pureza: Las materias primas deben ser de gran pureza.
- Baja resistencia a la fractura: El cuerpo sinterizado tiene menor tenacidad a la fractura y tiende a sufrir fractura transgranular.
- Límites del grano limpio: Esencialmente no hay fase líquida, y los límites de grano son relativamente "limpios".
- Resistencia estable a altas temperaturas: La resistencia a altas temperaturas se mantiene estable hasta 1600°C sin cambios significativos.
- Crecimiento del grano: A altas temperaturas, el crecimiento del grano es fácil, lo que provoca una escasa uniformidad del grano.
- Alta sensibilidad a las grietas: El material es muy sensible a la resistencia a la fisuración.
Propiedades del SiC sinterizado en fase líquida (LSiC):
- Menor temperatura de sinterización: En comparación con la sinterización en estado sólido, la temperatura de sinterización es inferior.
- Grano más pequeño: La granulometría es menor, con mejor uniformidad de granos.
- Mayor resistencia a la fractura: Debido a la introducción de una fase líquida en los límites de grano, el modo de fractura se desplaza hacia la fractura intergranular, mejorando significativamente la tenacidad a la fractura.
- Influencia aditiva: Utiliza óxidos eutécticos multicomponentes (por ejemplo, Y2O3-Al2O3) como aditivos de sinterización, favoreciendo la densificación.
- Reducción de la sensibilidad a las grietas: La sinterización en fase líquida reduce la sensibilidad del material a la resistencia a la fisuración.
- Unión de interfaz debilitada: La introducción de la fase líquida debilita la fuerza de unión en los límites de grano.
El carburo de boro sinterizado sin presión combina una gran pureza y las excelentes propiedades mecánicas del carburo de boro para su uso tanto en blindajes balísticos como en la fabricación de semiconductores.
Ventajas del SiC prensado en caliente:
- Permite la sinterización a temperaturas más bajas y tiempos más cortos, lo que da lugar a granos finos, alta densidad relativa y buenas propiedades mecánicas.
- El calentamiento y el prensado simultáneos facilitan la difusión por contacto de las partículas y la transferencia de masa.
- Adecuado para producir cerámicas de carburo de silicio con buenas prestaciones mecánicas.
Desventajas del SiC prensado en caliente:
- El equipo y el proceso son complejos.
- Altas exigencias al material del molde.
- Limitada a la producción de piezas de formas simples.
- Baja eficiencia de producción.
- Costes de producción elevados.
El carburo de silicio recristalizado (RSiC) es una cerámica de carburo de silicio puro fabricada mediante evaporación-condensación a alta temperatura, con una estructura porosa y de alta resistencia, que ofrece una excelente resistencia al calor, a la corrosión y al choque térmico, utilizada en mobiliario de hornos, boquillas y componentes químicos.
Propiedades y aplicaciones del SiC recristalizado:
- El proceso de sinterización, basado en la evaporación-condensación, no provoca contracción, lo que evita deformaciones o grietas.
- El RSiC puede moldearse mediante métodos como la fundición, la extrusión y el prensado, y su cocción sin contracción permite obtener dimensiones precisas.
- Después de la cocción, el RSiC recristalizado contiene 10%-20% de porosidad residual, principalmente influenciada por la porosidad del cuerpo verde, proporcionando una base para el control de la porosidad.
- El mecanismo de sinterización crea poros interconectados, lo que hace que el RSiC sea adecuado para aplicaciones de filtración de gases de escape y aire.
- El RSiC tiene límites de grano limpios, libres de impurezas de vidrio y metal, lo que garantiza una alta pureza y conserva las propiedades superiores del SiC para aplicaciones exigentes de alto rendimiento.
El carburo de silicio prensado isostáticamente en caliente (HIPSiC) es una cerámica de alto rendimiento producida mediante prensado isostático en caliente. Se somete a altas temperaturas (alrededor de 2000 ℃) y a una presión uniforme de gas de alta presión (normalmente argón), polvo de carburo de silicio se densifica en una estructura casi sin poros.
Ventajas del SiC prensado isostático en caliente:
- Microestructura uniforme y granulometría fina
- Baja temperatura y tiempo de sinterización
- Alta densidad
- Alta pureza y control de los componentes
Desventajas del SiC prensado isostático en caliente:
- Tecnología de envasado difícil
- Inversión inicial y costes operativos elevados
- Limitado para formas grandes o complejas
El carburo de silicio sinterizado por plasma de chispa es una cerámica de alto rendimiento producida mediante la tecnología de sinterización por plasma de chispa. Este proceso emplea corriente pulsada y presión para densificar rápidamente el polvo de carburo de silicio a temperaturas relativamente bajas (alrededor de 1800-2000 ℃) en poco tiempo.
Sinterización por plasma de chispa Propiedades del SiC:
- Mayor velocidad de calentamiento
- Menor temperatura de sinterización
- Menor tiempo de sinterización
- Granos finos y uniformes
- Alta densidad
- Aplicable a piezas pequeñas y de precisión
Mecanizado de cerámica de carburo de silicio
El carburo de silicio (SiC) es un material cerámico muy duradero con una dureza extrema (9,5 Mohs), estabilidad térmica (hasta 1650 ℃) y resistencia al desgaste, la corrosión y las altas temperaturas. Sin embargo, el mecanizado del carburo de silicio presenta dificultades debido a su extrema dureza y fragilidad. Se necesitan técnicas y herramientas especializadas para conseguir cortes y formas precisos. Los métodos de mecanizado más comunes son:
- Rectificado con diamante: Las herramientas de diamante se utilizan para conseguir superficies lisas y formas precisas.
- Corte por láser: Adecuado para cortar materiales SiC finos. El corte por láser ofrece alta precisión y un desperdicio mínimo de material.
- Mecanizado por ultrasonidos: Este método utiliza vibraciones de alta frecuencia para cortar y dar forma a materiales frágiles como el SiC sin provocar grietas.
- Mecanizado por descarga eléctrica (EDM): Un método no tradicional que utiliza chispas eléctricas para eliminar material, eficaz para cerámicas duras como el SiC.
- Rectificado con herramientas CBN: Las herramientas de nitruro de boro cúbico (CBN) pueden utilizarse para el rectificado de SiC, constituyendo una alternativa al rectificado con diamante para determinadas aplicaciones.
- Corte por chorro de agua: Utilización de un chorro de agua a alta presión, a veces con partículas abrasivas, para cortar SiC. Este método es útil para cortar formas complejas.
Envases cerámicos de carburo de silicio
Los productos cerámicos de carburo de silicio suelen envasarse en bolsas selladas al vacío para evitar la humedad o la contaminación y se envuelven con espuma para amortiguar las vibraciones y los impactos durante el transporte, lo que garantiza la calidad de los productos en su estado original.
Descargar
Solicitar presupuesto
Lo comprobaremos y le responderemos en 24 horas.