Zirconia Ceramic Substrate
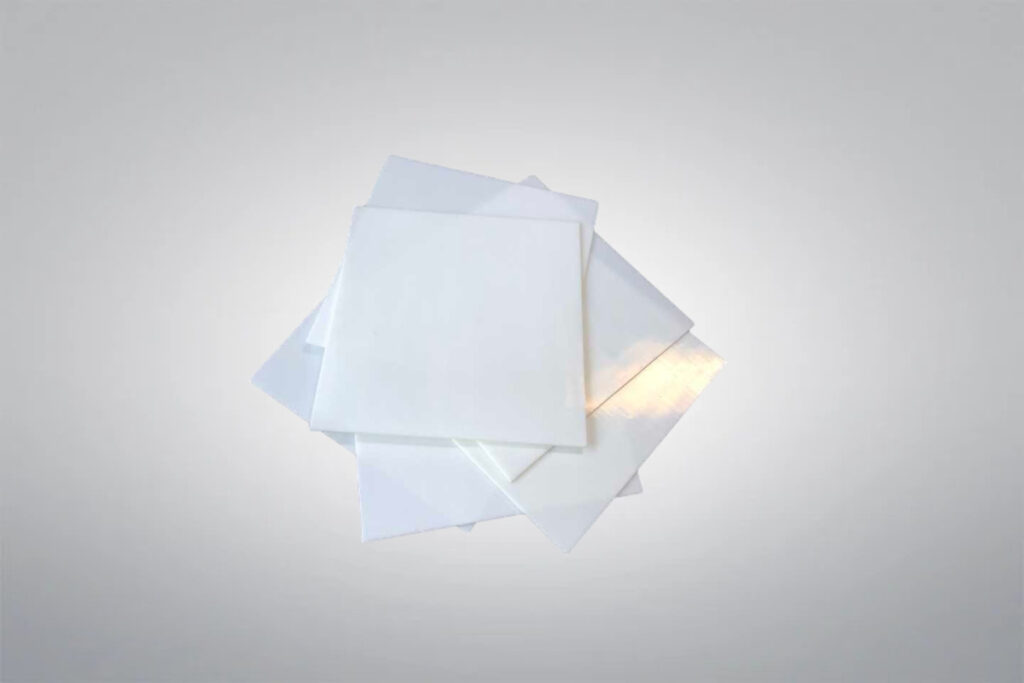
Zirconia Ceramic Substrate
Purity: ≥99%
Zirconia Ceramic Substrate is a high-performance material known for its outstanding high-temperature resistance, electrical insulation, and low dielectric loss. It offers excellent thermal conductivity and chemical stability, making it suitable for applications in electronics and circuit components. Its ability to withstand harsh environments and maintain stability under thermal and electrical stress makes it a reliable choice for advanced technology applications. We can supply high-quality zirconia ceramic substrates with various specifications and competitive prices, offering customized solutions to meet specific requirements.
Or email us at sales@heegermaterials.com.Zirconia Ceramic Substrate Data Sheet
Reference Code: | HM2609 |
Purity: | ≥99% |
Color: | White |
Chemical Formula: | ZrO2 |
Material Grades: | Ultra Tough Grade, Ultra Tough HIP Grade, 3YZ Ceramic Grade, Nano HIP Grade |
Maximum Operating Temperature: | 900°C |
Dimensions: | Within 100×100×1.0 mm, or customized |
Material: | ZrO2: 94.8±0.5%, Y2O3: 5.2±0.5%, or customized |
Precision: | ±0.001 mm |
Polishing: | Single or double polishing |
Zirconia Ceramic Substrate Description
Zirconia Ceramic Substrate is a premium material valued for its exceptional high-temperature resistance, excellent electrical insulation, low dielectric constant, and minimal dielectric loss. It also boasts high thermal conductivity and outstanding chemical stability, making it ideal for demanding applications. With a thermal expansion coefficient closely matching that of components, it ensures compatibility and reliability in electronic circuits and components. Zirconia Ceramic Substrates are available in die-cast and laser-scribed variations, offering versatility for various applications. We can provide high-precision, competitively priced zirconia ceramic substrates, along with other ceramic materials such as Alumina (Al2O3), Aluminium Nitride (AlN), Silicon Carbide (SiC), and Boron Nitride (BN) to meet diverse needs.
Zirconia Ceramic Substrate Features
- High-Temperature Resistance: Zirconia ceramic substrate can withstand extreme temperatures, maintaining its structural integrity in harsh environments.
- Excellent Electrical Insulation: It provides superior electrical insulation, making it ideal for electronic and electrical applications.
- Low Dielectric Constant and Loss: This material offers a low dielectric constant and minimal dielectric loss, ensuring efficient signal transmission in electronic devices.
- High Thermal Conductivity: Zirconia ceramic substrates excel in thermal management, efficiently dissipating heat in high-power applications.
- Chemical Stability: The material is highly resistant to chemical corrosion, ensuring long-lasting performance even in aggressive environments.
- Thermal Expansion Compatibility: Its coefficient of thermal expansion closely matches that of many electronic components, preventing stress and damage during thermal cycling.
- Versatile Processing Options: Available in die-cast and laser-scribed forms, providing flexibility in manufacturing processes for various applications.
Zirconia Ceramic Substrate Applications
- Electronics and Circuit Boards: Used in the manufacturing of electronic substrates for devices requiring high insulation and heat resistance, such as power modules and hybrid circuits.
- LED and Optoelectronics: Ideal for applications in LED lighting and optoelectronic devices, where high thermal conductivity and electrical insulation are essential.
- High-Power Electronics: Used in power electronics like power semiconductors, where heat dissipation and insulation are critical.
- Aerospace and Automotive: Zirconia Ceramic Substrates are employed in the aerospace and automotive industries for sensors, actuators, and other high-temperature applications.
- Medical Devices: Utilized in the production of medical devices that require high chemical stability and electrical insulation, such as sensors and diagnostic equipment.
Zirconia Material Properties
Zirconia Material Grades
Ultra Tough Grade is a highly advanced zirconia ceramic composite material that combines partially stabilized zirconia with an enhanced crystal structure to achieve exceptional mechanical properties.
General Properties
- Operates at temperatures up to 1500°C
- Fully sintered for a pore-free structure
- High fracture toughness and impact resistance without compromising bending strength or hardness
- Enhanced resistance to crack propagation due to its unique microstructure
- Increased resistance to hydrothermal aging with Ceria partial stabilization
Applications
- High-pressure equipment such as ball valve balls and seats
- Ultra-high-pressure pumping elements
- Flow control devices for high-pressure equipment like homogenizers
- Deep well down-hole valves and seats
- Rollers and guides for metal forming
Ultra Tough HIP Grade is a cutting-edge composite material that has undergone Hot Isostatic Pressing (HIP) to achieve superior strength, toughness, and reliability, making it ideal for challenging applications.
General Properties
- Operates at temperatures up to 1500°C
- HIP-processed for exceptional strength and consistency
- High fracture toughness combined with excellent bending strength and hardness
- Superior crack deflection properties in a partially stabilized zirconia matrix
- Enhanced resistance to hydrothermal aging with Ceria partial stabilization
Applications
- High-pressure equipment like valve balls and seats
- Ultra-high-pressure pumping elements
- Flow control components for high-pressure homogenizers
- Deep well down-hole valves and seats
- Rollers and guides for metal forming
The 3YZ Ceramic Grade, based on 3 mol % Yttria Partially Stabilized Zirconia (3YSZ), provides a finer grain structure for enhanced mechanical properties and superior isotropy.
General Properties
- Operates at temperatures up to 1000°C
- Low thermal conductivity for temperature stability
- Excellent chemical inertness, particularly in molten metal environments
- High wear resistance and fracture toughness
- High hardness for demanding mechanical applications
Applications
- High-pressure equipment like ball valve balls and seats
- Ultra-high-pressure pumping elements
- Flow control devices for high-pressure homogenizers
- Deep well down-hole valves and seats
- Rollers and guides for metal forming
Nano HIP Grade features a 3 mol % Yttria Partially Stabilized Zirconia (3YSZ) with an ultrafine grain structure, densified through Hot Isostatic Pressing (HIP) for exceptional reliability and performance.
General Properties
- Operates at temperatures up to 1000°C
- Low thermal conductivity for better thermal management
- Outstanding chemical resistance, particularly in molten metals
- High wear resistance and excellent fracture toughness
- Ultra-fine grain structure providing high hardness and superior performance
Applications
- High-pressure equipment such as valve balls and seats
- Ultra-high-pressure pumping elements
- Flow control components for high-pressure homogenizers
- Deep well down-hole valves and seats
- Rollers and guides for metal forming
Zirconia Ceramic Machining
Zirconia, a high-performance ceramic, is known for its toughness, hardness, and wear resistance, making it ideal for applications requiring high mechanical strength and thermal stability. However, machining zirconia can be challenging due to its hardness and toughness, requiring different methods depending on its processing state.
Machining Zirconia in Different States:
- Green and Biscuit Form: Easier to machine before sintering, but tight tolerances can’t be maintained due to shrinkage during sintering.
- Fully Sintered Zirconia: Becomes hard and dense, requiring diamond grinding or cutting for precise shapes.
Common Machining Methods:
- CNC Machining: Used for complex shapes, often with diamond tools.
- Diamond Grinding: For precise dimensions and surface finish.
- Diamond Cutting and Sawing: Special diamond tools prevent cracking.
- Polishing: Smooths surfaces, especially for medical or precision applications.
Zirconia Ceramic Packaging
Zirconia ceramic products are typically packaged in vacuum-sealed bags to prevent moisture or contamination and wrapped with foam to cushion vibrations and impacts during transport, ensuring the quality of products in their original condition.
Download
Get A Quote
We will check and get back to you in 24 hours.