Alumina Ball
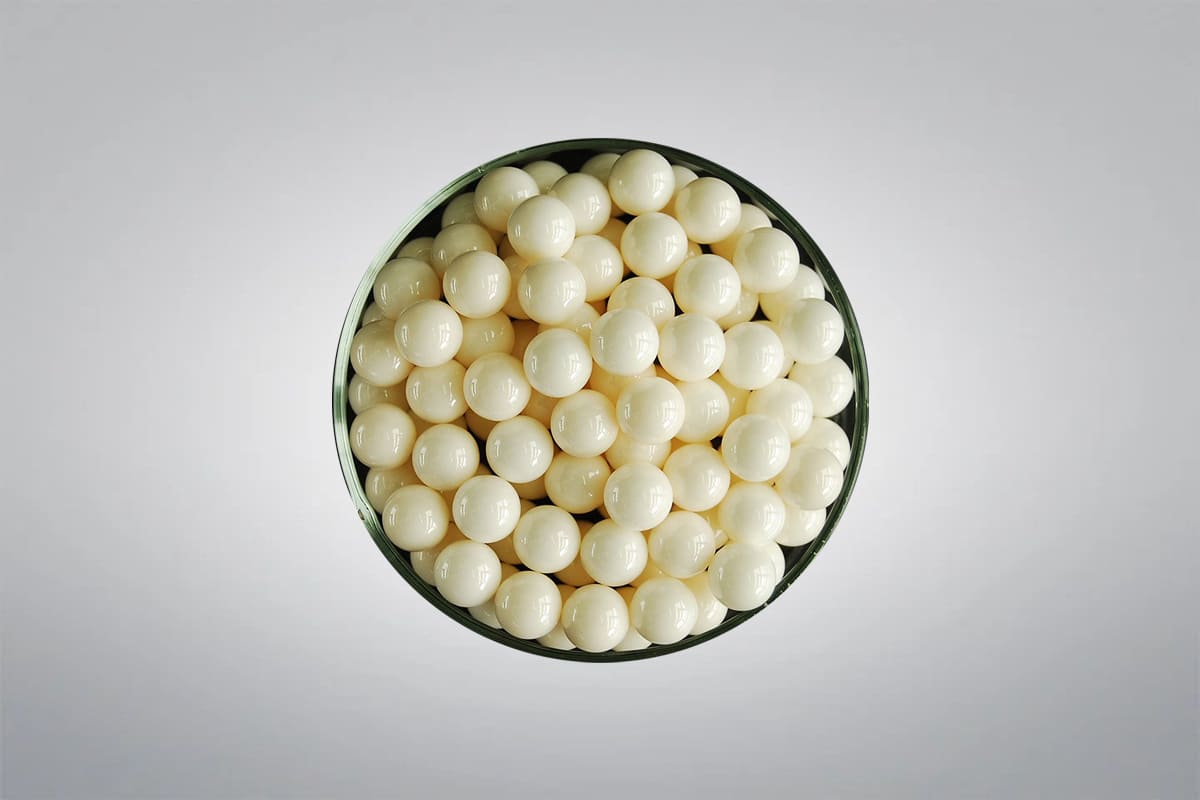
Alumina Ball
Purity: 95%, 96%, 99%, 99.5%, 99.7%, 99.95%
Diameter: 0.8-100 mm, or customized
Alumina Ball is a high-performance ceramic material primarily composed of alumina with the purity ranging from 90%-99.9%. The additives is designed to enhance its properties. It is widely used as grinding media, catalyst support, chemical packing material, and wear-resistant linings. As a leading supplier and manufacturer of premium alumina products, we can supply high-quality alumina balls with various specifications and competitive prices, offering customized solutions to meet specific requirements.
Or email us at sales@heegermaterials.com.Alumina Ball Data Sheet
Reference Code: | HM1985 |
Purity: | 95%, 96%, 99%, 99.5%, 99.7%, 99.95% |
Color: | White |
Density: | 3.7-3.98 g/cm3 |
Diameter: | 0.8-100 mm, or customized |
Alumina Ball
Alumina Ball is made from high-purity aluminum oxide (Al2O3) with typical purities ranging from 90%-99.9%. It has been proven to have superior wear performance in corrosive environments and high-temperature conditions. It resists oxidation and is tolerant to high moisture environments, salt solutions, and many chemicals. These excellent properties make it widely applied in ball mills, chemical twoers, and high-temperature equipment. Advanced Ceramics Hub can supply customized solutions for diameter and surface finish to meet diverse industrial and research requirements.
Alumina Ball Advantages
- Excellent electrical insulation properties
- High hardness and mechanical strength
- Wear and abrasion-resistant
- High thermal conductivity and thermal shock resistance
- Low density
- Resistant to strong acid and alkali attack at high temperatures
- Transparent to microwave radio frequencies
- High compressive and dielectric strength
- Very specific thermal conductive and thermal expansion rates
Alumina Ball Applications
- Grinding Media: Used in ball mills to grind ceramic raw materials, ores, and pigments, leveraging their high hardness (Mohs 9) and wear resistance to minimize contamination and boost efficiency.
- Catalyst Support: Serve as a support material for catalysts in chemical and petroleum refining processes, thanks to their high surface area, heat resistance (up to 1700°C), and chemical stability.
- Packing Material: Employed as packing in chemical towers (e.g., distillation or absorption columns) to enhance mass transfer efficiency, owing to their corrosion resistance and thermal stability.
- Wear-Resistant Linings: Applied as linings in pipelines, hoppers, or equipment to protect against abrasion, especially in mining and cement industries.
- Valves and Seals: Used as ball valves or sealing components in pump systems, extending service life due to their high strength and corrosion resistance.
- High-Temperature Insulation: Utilized in high-temperature furnaces or kilns as insulation or support materials, benefiting from low thermal conductivity and excellent thermal stability.
Alumina Material Properties
Alumina Material Grades
It has a very high purity (99.95%) grade of Alumina (Aluminum Oxide) exhibiting an exceptional combination of mechanical and electrical properties. It features very high hardness, exceptional electrical resistivity, high-temperature mechanical stability and strength in addition to corrosion resistance and bio/chemical inertness.
Its high-temperature stability and electrical stability make it particularly suitable for high-temperature applications such as high voltage/frequency insulators, heating elements supports, etc
Physical Properties:
- Color: White
- Density: 3.98 g/cm3
Applications:
- High-temperature electrical insulators
- Very high voltage/frequency insulators
- Machine components where high wear resistance
is required in an oxidizing environment - Precision shafts in high-wear condition
- Unlubricated (vacuum) or gas/water lubricated
high speed sliding bearings - Shot blast nozzles
- Abrasive flow deflector plates/cones
- Valve seats
- Wire guides
It’s a high-purity grade of Alumina (Aluminum Oxide) and one of the high-performance grades in this range of materials. It features a 99.7% purity Alumina base material that provides a superior set of mechanical and electrical properties while maintaining a reasonable cost. It is a very hard-wearing technical ceramic offering and is ideally suited to a wide range of industrial applications where mechanical and electrical performance is of the essence and the material needs to perform adequately in aggressive environments.
It can be machined in the “green state”- that is before sintering takes place, thus ensuring a large variety of shapes and sizes. It can also be diamond ground to tight tolerances in the fully sintered state using diamond grinding.
Physical Properties:
- Color: Ivory
- Density: 3.9 g/cm3
Applications:
- Electronic components & substrates
- High-temperature electrical insulators
- High voltage insulators
- Laser tubes
- Machined components
- Mechanical seals
- Precision shafts and axles in high-wear environments
- Roller and ball bearings
- Seal rings
- Semiconductor parts
- Shot blast nozzles
- Thermocouple tubes
- Tap plates
- Valve seats
- Wear components
- Wire and thread guides
- Ballistic Armor
99.5% Purity Alumina is a high-performance engineering material with exceptional mechanical strength, high-temperature resistance, and excellent electrical insulation properties. It is widely used in industrial equipment, electronic components, medical devices, and aerospace applications.
Physical Properties:
- Color: Ivory
- Density: 3.9 g/cm3
Applications:
- Electronic components & substrates
- High-temperature electrical insulators
- High voltage insulators
- Laser tubes
- Machined components
- Mechanical seals
- Precision shafts and axles in high-wear environments
- Roller and ball bearings
- Seal rings
- Semiconductor parts
- Shot blast nozzles
- Thermocouple tubes
- Tap plates
- Valve seats
- Wear components
- Wire and thread guides
- Ballistic Armor
99% Purity Alumina Is a premium industrial ceramic material with excellent mechanical properties, ultra-high hardness, high-temperature resistance, and insulation performance. It can maintain stable chemical and physical properties even in extreme environments, making it widely used in semiconductors, electronic components, laser technology, and aerospace.
Physical Properties:
- Color: Ivory
- Density: 3.85 g/cm3
Applications:
- Electronic components & substrates
- High-temperature electrical insulators
- High voltage insulators
- Laser tubes
- Machined components
- Mechanical seals
- Precision shafts and axles in high-wear environments
- Roller and ball bearings
- Seal rings
- Semiconductor parts
- Shot blast nozzles
- Thermocouple tubes
- Tap plates
- Valve seats
- Wear components
- Wire and thread guides
- Ballistic Armor
It is a regular purity grade Alumina (Aluminum Oxide) and it is one of the workhorses of the technical ceramics industry. It features a 96% purity Alumina base material providing a balanced “cost to quality” ratio. It is a hard-wearing technical ceramic offering an excellent combination of both mechanical and electrical properties and is ideally suited to a wide range of industrial applications where cost is of the essence, but the material still needs to perform adequately from a mechanical and electrical standpoint.
It can be machined in the “green state”- that is before sintering takes place, thus ensuring a large variety of shapes and sizes. It can also be diamond ground to tight tolerances in the fully sintered state using diamond grinding.
Physical Properties:
- Color: White
- Density: 3.75 g/cm3
Applications:
- Electronic components & substrates
- High-temperature electrical insulators
- High voltage insulators
- Laser tubes
- Machined components
- Mechanical seals
- Precision shafts and axles in high-wear environments
- Roller and ball bearings
- Seal rings
- Semiconductor parts
- Shot blast nozzles
- Thermocouple tubes
- Tap plates
- Valve seats
- Wear components
- Wire and thread guides
- Ballistic Armor
95% Purity Alumina is an economical and practical engineering material. Its slightly lower alumina content reduces production costs while maintaining decent wear resistance and processing flexibility. It is commonly used in mechanical parts, electrical insulators, and wear-resistant bushings, offering an excellent cost-performance balance.
Physical Properties:
- Color: White
- Density: 3.7 g/cm3
Applications:
- Electronic components & substrates
- High-temperature electrical insulators
- High voltage insulators
- Laser tubes
- Machined components
- Mechanical seals
- Precision shafts and axles in high-wear environments
- Roller and ball bearings
- Seal rings
- Semiconductor parts
- Shot blast nozzles
- Thermocouple tubes
- Tap plates
- Valve seats
- Wear components
- Wire and thread guides
- Ballistic Armor
Alumina Ceramic Machining
Alumina ceramics are produced through methods such as injection molding, die pressing, isostatic pressing, slip casting, and extrusion. After sintering and densification, machining requires diamond grinding techniques. Advanced Ceramic Hub utilizes cutting-edge green and biscuit machining technology to produce more complex components with traditional methods. Our advanced machining center includes drilling, grinding, milling, polishing, sawing, tapping, threading, and turning, enabling the manufacture of alumina ceramic components with tight tolerances and high complexity. During the machining process, the following precautions should be observed:
- Shrinkage Control: Alumina ceramics shrink by about 20% during sintering, requiring dimensional adjustments in the green body stage.
- Tolerance Control: Precise tolerances are unachievable in the green or pre-sintered state; fine machining should follow sintering.
- Diamond Grinding: Post-sintering, high-hardness alumina requires diamond grinding, as conventional methods fall short.
- Tool Selection: Diamond-coated tools or grinding wheels are essential to handle ceramic hardness and prevent tool damage.
- Temperature Control: Strict temperature management during sintering prevents cracking or deformation.
- Stress Management: Excessive stress during machining must be avoided to prevent brittle failure.
- Cutting Speed and Feed Rate: Controlled speeds and feeds ensure quality and extend tool life.
- Surface Treatment: Post-machining polishing removes defects, enhancing performance and appearance.
Alumina Ceramic Packaging
Alumina Ceramic products are typically packaged in vacuum-sealed bags to prevent moisture or contamination and wrapped with foam to cushion vibrations and impacts during transport, ensuring the quality of products in their original condition.
Download
Get A Quote
We will check and get back to you in 24 hours.