Applications of Silicon Carbide in Electronics
Silicon Carbide (SiC) is a semiconductor material known for its exceptional physical, chemical, and electrical properties. Composed of silicon and carbon, SiC boasts high thermal conductivity, mechanical strength, and resistance to high temperatures. Compared to traditional silicon materials, SiC’s wide bandgap allows it to operate stably in extreme conditions such as high frequency, high voltage, and high temperature environments. This makes SiC a valuable material in power electronics, RF electronics, high-temperature devices, and power conversion systems.
In recent years, SiC has become increasingly important in electronics due to the global emphasis on energy efficiency and environmental protection. Its widespread use in electric vehicles, solar and wind energy systems, and its unique advantages in high-temperature and high-power applications have made SiC a key material for many cutting-edge technologies. Moreover, with the ongoing reduction in SiC production costs, its commercial application prospects are becoming more promising, and it is expected to play a significant role in the upcoming electronic technology revolution.
At Advanced Ceramics Hub, we specialize in high-quality silicon carbide products, ensuring optimal performance for industrial and scientific applications.
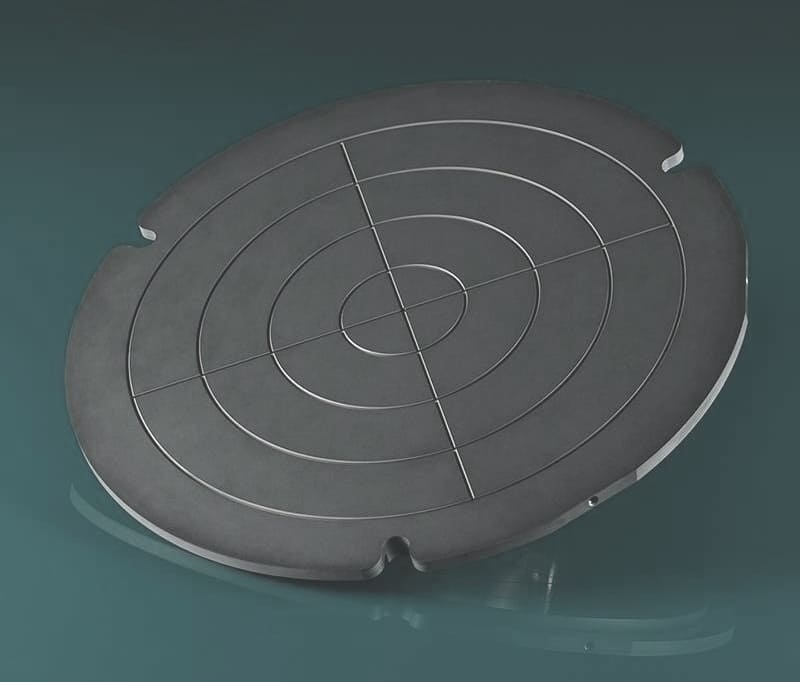
Basic Properties of Silicon Carbide
Silicon Carbide (SiC) is a semiconductor material known for its outstanding physical and electrical properties, making it essential in advanced technological applications. With its high thermal conductivity, mechanical strength, and wide bandgap, SiC is widely used in fields ranging from power electronics to aerospace. The material’s unique structural characteristics, including its crystal forms and density, further contribute to its versatility and efficiency in demanding environments. Below are the key properties of SiC:
1. High Thermal Conductivity
SiC exhibits high thermal conductivity, allowing for effective heat dissipation, which helps maintain electronic device stability. Compared to traditional silicon materials, SiC performs better in heat management in high-power and high-temperature applications.
- Melting Point: Sublimes at 2,830°C (does not melt)
- Thermal Conductivity: 4H-SiC: 490 W/m·K (parallel to c-axis), and 3× better than copper at room temp
- Thermal Expansion: 4.2 ppm/K (matches well with semiconductors)
2. Superior Electrical Properties
With a wide bandgap (approximately 3.26 eV), SiC can withstand higher voltage and frequency, making it an ideal material for high-voltage and high-frequency applications. It is crucial in power electronics and RF electronics.
Parameter | 4H-SiC | Silicon | Advantage |
Bandgap | 3.2 eV | 1.1 eV | Enables high-voltage devices |
Breakdown Field | 3 MV/cm | 0.3 MV/cm | 10× higher than Si |
Electron Mobility | 900 cm²/V·s | 1,400 cm²/V·s | Balances speed & power |
3. Mechanical Strength
SiC possesses exceptional mechanical strength, enabling it to endure heavy loads and extreme conditions. This makes SiC suitable for applications requiring wear resistance and pressure tolerance, such as in the automotive and aerospace industries.
Property | Value | Significance |
Hardness | 9.5 Mohs | 2nd hardest commercially available material after diamond |
Flexural Strength | 300-600 MPa | Comparable to tungsten carbide |
Young’s Modulus | 400-450 GPa | 3× stiffer than steel |
4. High Temperature Resistance
SiC can operate at extremely high temperatures, typically up to 1600°C, much higher than the temperature limits of traditional silicon materials. This property makes SiC valuable in high-temperature environments, such as in automotive engines and aerospace devices.
Property | Value | Significance |
Thermal Conductivity @ 1,000°C | 100 W/m·K | Outperforms metals (stainless steel: ~25 W/m·K) |
Thermal Shock Resistance | ΔT > 500°C | Survives rapid quenching (Al₂O₃ fails at ΔT ~200°C) |
Creep Resistance | <0.1% strain @ 1,400°C/100MPa | Maintains structural integrity |
5. Chemical Properties
- Oxidation Resistance: Forms protective SiO₂ layer at 1,200°C
- Chemical Inertness: Resists most acids/alkalis (except HF)
- Corrosion Rate: <0.1 mm/year in molten salts (900°C)
Comparison to Other Materials:
Property | SiC (4H) | Si | GaN | Ga₂O₃ | Diamond | AlN (Ceramic) | SiO₂ (Ceramic) | Cu (Metal) |
Bandgap (eV) | 3.2 | 1.1 | 3.4 | 4.8 | 5.5 | 6.2 | 9.0 | 0 (Conductor) |
Breakdown Field (MV/cm) | 3.0 | 0.3 | 3.3 | 8.0 | 10.0 | 1.5 | 0.5 | N/A |
Thermal Conductivity (W/m·K) | 490 | 150 | 130 | 27 | 2000 | 285 | 1.4 | 400 |
Electron Mobility (cm²/V·s) | 900 | 1400 | 2000 | 300 | 2200 | <1 | <1 | N/A |
Saturation Velocity (×10⁷ cm/s) | 2.0 | 1.0 | 2.5 | 1.5 | 2.7 | N/A | N/A | N/A |
Max Operating Temp (°C) | 600 | 150 | 300 | 500 | 800 | 1000 | 1700 | 1085 (M.P.) |
Melting/Sublimation Point (°C) | 2830 | 1414 | 2500* | 1900 | 4027 | 2200 | 1713 | 1085 |
Hardness (Mohs) | 9.5 | 6.5 | ~8.5 | ~8 | 10 | 9 | 7 | 2.5-3 |
Dielectric Constant | 9.7 | 11.7 | 9.0 | 10 | 5.7 | 8.5 | 3.9 | N/A |
CTE (ppm/K) | 4.2 | 2.6 | 5.6 | 7.5 | 1.1 | 4.5 | 0.5 | 17 |
Cost (Relative) | $$$ | $ | $$$$ | $$ | $$$$$ | $$ | $ | $ |
Looking for top-quality silicon carbide products? Explore Advanced Ceramics Hub’s selection.
Key Applications of Silicon Carbide (SiC) in Electronics
1. Applications in Power Electronics
SiC’s superior material properties—wide bandgap (3.3 eV), high thermal conductivity (~4.9 W/cm·K), and high breakdown field strength (2-3 MV/cm)—make it ideal for high-power, high-frequency, and high-temperature applications. Below are its major applications in power electronics:
Key Advantages:
- Higher Efficiency
- High Voltage and Temperature Tolerance
- Compact Size and Weight Reduction
Key Applications:
✅ SiC Diodes and MOSFETs:
SiC Diodes
- Used in power rectifiers for low forward voltage drop and fast switching speeds.
- Ideal for high-efficiency power supplies and converters.
SiC MOSFETs
- Key components in modern power electronics, especially for high-voltage applications.
- Allow faster switching speeds and higher power densities, improving system efficiency and performance.
✅ Electric Vehicles (EVs):
Efficient Inverters:
- Convert DC power from the battery to AC power for the motor.
- SiC components enable higher switching frequencies, improving efficiency, reducing size, and extending driving range.
Faster Charging:
- SiC-based chargers handle higher voltages and currents, reducing charging time.
Enhanced Battery Management Systems:
- SiC’s fast-switching capability improves battery charge and discharge monitoring, enhancing performance and longevity.
✅ Solar and Wind Energy Systems:
Power Conversion:
- SiC power electronics are used in inverters to convert DC energy from solar panels or wind turbines into AC power.
- High efficiency and ability to handle high voltages make the system more efficient and reliable.
Improved Grid Integration:
- SiC components allow faster and more stable control of power flows, enhancing grid integration, especially in distributed generation systems.
Reduced System Costs:
- SiC-based inverters reduce system costs by improving efficiency and reducing the size of equipment and cooling requirements.
2. Applications in RF Electronics
SiC’s wide bandgap (3.3 eV), high breakdown voltage (2-3 MV/cm), and excellent thermal conductivity (~4.9 W/cm·K) make it ideal for high-power, high-frequency RF applications, especially where efficiency and thermal management are critical.
✅ RF Power Amplifiers
- 5G Base Stations: SiC-based RF amplifiers enable higher power density and efficiency for mmWave and sub-6GHz networks.
- Radar Systems: Used in military, aerospace, and automotive radar (e.g., AESA radars) due to high power handling and thermal stability.
- Satellite Communications: Supports high-frequency (Ka/Q-band) and high-power RF transmission for space applications.
✅ High-Frequency Signal Processing
- Microwave & mmWave Circuits: SiC substrates improve performance in mixers, oscillators, and filters for telecom and defense.
- Electronic Warfare (EW): Used in jamming systems and signal intelligence (SIGINT) due to high power and ruggedness.
✅ Wireless Power Transmission
Long-range wireless power transfer (e.g., drone charging, space-based solar power) benefits from SiC’s high-frequency efficiency.
✅ Medical & Scientific RF Systems
- MRI & Plasma Generation: SiC devices handle high-voltage RF pulses in medical imaging and industrial plasma systems.
3. Applications in High-Temperature Electronics
SiC’s exceptional thermal stability (operating up to 600°C), high thermal conductivity (4.9 W/cm·K), and radiation hardness make it the material of choice for extreme-environment applications:
✅ Aerospace & Defense Systems
- Jet engine monitoring sensors – Withstands 500°C+ exhaust temperatures
- Spacecraft power electronics – Operates in radiation-heavy space environments
- Hypersonic vehicle electronics – Handles extreme aerodynamic heating
✅ Automotive Electronics
- Electric vehicle powertrains – Under-hood components near combustion engines
- Exhaust gas sensors – Direct mounting in hot exhaust streams
- Brake-by-wire systems – High-temp operation near braking components
✅ Energy & Industrial System
- Downhole drilling electronics – Operates in 300°C+ oil/gas wells
- Nuclear reactor monitoring – Radiation-resistant sensors and controls
- Industrial furnace controls – Withstands prolonged high-temp exposure
Request a custom quote for high-quality silicon carbide products.
What Are The Key Development Directions of Silicon Carbide Technology?
1. Material & Fabrication Advancements
- Wafer Size Scaling: Transition from 150mm to 200mm wafers (expected 2024-2026), reducing costs by ~30%
- Defect Reduction: Dislocation density target <100 cm⁻² for improved yield (current: 500-1000 cm⁻²)
- Novel Epitaxial Growth: Atomic-layer deposition (ALD) for ultra-uniform 200+ μm epi-layers
2. Application-Specific Breakthroughs
A. Electric Vehicles
- Integrated Powertrain Modules:
Combining an inverter, OBC, and DC-DC in single SiC package (e.g. VW’s MEB+ platform) - 48V SiC Systems:
Enabling 10kW+ ancillary power networks
B. Quantum & Cryogenic
- 4K operation for quantum computing power delivery
- Superconducting grid interfaces
3. Integration & Packaging
- Embedded Die Solutions: Direct SiC die attach to copper substrates (ΔTj <15°C/mm²)
- 3D Power Modules: Stacked SiC+GaN configurations for 10kW/cm³ density
- Self-Cooling Designs: Microfluidic channels integrated with SiC dies
4. Sustainability Drivers
CO₂ Reduction Potential:
- 1.5B tons cumulative savings in EVs (2025-2035)
- 30% lower lifetime emissions vs Si per kW
Circular Manufacturing: 95% SiC wafer recycling rate target
Silicon Carbide (SiC) has emerged as a crucial material in modern electronics due to its unique properties, including its wide bandgap, high thermal conductivity, and robustness in high-power and high-temperature environments. Its applications span across a wide range of sectors, including electric vehicles, renewable energy systems, telecommunications, and industrial power electronics. As the demand for more efficient, durable, and high-performance components increases, SiC is positioned to be a key enabler of future technological advancements.
The future potential of SiC lies in its ability to transform industries by improving the efficiency and performance of devices, reducing energy losses, and enabling the development of more sustainable systems. With ongoing research and technological advancements, SiC-based devices are expected to play a leading role in emerging fields such as electric vehicle powertrains, renewable energy grids, and high-frequency communication systems.
Looking for premium ceramic heaters? Contact us today!